Introduction
Agricultural mechanization is a major breakthrough in the evolution of technology implementation in agricultural machinery. In this way, it is used to satisfy and optimize the needs in the field, in order to obtain a greater operational capacity. As a result, the ergonomics of work and practicality in the operation of the machinery are significantly increased, minimizing wasted time and money (1).
Sprayers are implements used in the application of agricultural pesticides, which are directly related to the form, quality and uniformity with which these products are applied. In this context, the correct use of the application technology is essential for greater efficiency of operation of these machines. Thus, calibration and regulation provide a correct rate of application, reduction of risk of drift and satisfactory coverage of targets for the success of phytosanitary control (2).
According to Barcellos et al. (3), the effects of the vertical oscillations of the bar alter its height in relation to the target originated by irregularities in the terrain, which affects the distribution of the syrup. Thus, the overlap is defined as the uniformity of the sprayed jets of each end along the bar in the longitudinal and transverse directions. This parameter is determined according to the spacing between the nozzles, tip opening angle, bar height and working pressure, among others (4). Thus, it is necessary that these elements are interacted in order that the syrup is distributed homogeneously on a given target (5).
The excess deposition of the liquid or a low deposited amount are undesirable cases. And the simplest way to avoid them is to ensure the parallelism of the spray bar to the sprayed surface. However, at the time of application, the parameters must be respected in order to provide an overlapping compliance and thus mitigate drift, pointing to one of the major problems of pesticide application (6). As a consequence, Al Heidary et al. (7) explained that drift is a complex phenomenon because it results from a combination of several factors. These factors can be separated into three groups: (a) characteristic of spray droplets, such as droplet size and velocity, and physical and chemical characteristics of the spray; (b) operating conditions such as bar height, working pressure and speed; (c) weather conditions, such as temperature, relative humidity and wind speed.
In this context, the use of embedded technology is promising, since it allows electronic circuits to have contact with the environment and perform actions according to their attributions. In this sense, the use of the set of electronic systems, composed of (hardware) and (software), allows acquisition, processing, storage and communication of data. Thus, the use of sensors can be one of the alternatives to reduce drift and to control and monitor the spray bar to improve the performance of pesticide applications (8).
Automation in agricultural machinery is wide, and there is a vast capacity of these technologies acting in several areas. Nowadays it is notable that several important researches in the area of embedded electronics are being developed, using intelligent systems innovation, to make feasible application of this technology in agricultural machinery and equipment. In this paper, we have developed feasible solutions for the development of intelligent automation and application systems, such as Bakker et al (9), Griepentrong et al (10), Dong et al (11), et al. (12) embedded systems that perform more precise and faster operations to reduce cost and increase work optimization.
However, there is little research that has been carried out with the use of sensors with the function of detecting bar height at the moment of spraying, while maintaining the same parallelism with respect to the target.
The aim of this work is to develop a system for the constant monitoring of the vertical oscillation of the agricultural sprayer bar, obtaining data of relative humidity, air temperature and bar height in sprayers.
Material and methods
The work was carried out at the Lageado Experimental Farm, at the Laboratory of Machines for Spraying the Testing Nucleus of Machines and Agricultural Tires (NEMPA), UNESP-FCA, Campus of Botucatu, São Paulo.
The system used allows the use of a generalized and universal form, and can be implanted in the other models of agricultural sprays of the market, with few modifications. Therefore, a set of hardware consisting of Arduino uno, Protoboard, Jumper, Ultrasonic Sensor HC-SR04, DHT22 Temperature and Humidity Sensor, 20x4 Blue Backlight LCD Display, as described in figure 1. The development of the programming was executed in the ARDUINO WEB EDITOR software, which described the command code for the operation of each of the sensors and components.
An assay was performed to analyze variations in spraybar height by mechanized spraying using a Honda Fourtrax quadricycle equipped with a 3 m spray bar and a mean velocity of 6 km h -1. The spray tip model AIXR11002, nozzle spacing 0.50 m, totaling 6 nozzles was used, the spray bar was positioned at a height of 0.60 m in relation to the ground Operating at the working pressures of 200 kPa (2 bar ).
The experiment to verify vertical bar height oscillation was conducted in four treatments with three replicates (table 1). The treatments were composed by the quadriculo path, in a field with (C) and without (S) obstacle (OBS), all the treatments and the paths were covered with (C) and without (S) spraying (PUL). The movement of the bar was evaluated through Simove, which was installed with different sensors, such as temperature and relative humidity, with the purpose of collecting the respective data, and with two ultrasonic sensors, one in the middle and the other at the end of the bar , with the function of informing the height of the bar, all this information was collected and stored in a database of the developed system, constantly during the course of the sprayer.
The terrain with obstacle was an area in which the soil was first prepared (plowing), with that, all the routes were made in the same path, but each step compacted the soil. Thus, each pass showed small variations in the sensor readings, due to the oscillation of the bar, but did not significantly alter the data collected by the sensors.
The treatment without obstacle was performed on a dirt road (unpaved), so the terrain was flat, but with few irregularities in the relief, causing the sprayer bar to move, simulating a real spraying condition, however, did not significantly affect the data. The influence with and without spraying of the syrup was also analyzed, and the treatments were only sprayed with water.
The results were submitted to analysis of variance and studied the interaction between the systems and conditions, followed by the Tukey test at 5% of probability.
Results and discussion
Table 2 shows the average data found in the readings performed during the course.
Table 2 Descriptive statistics of the analyzed variables. Arithmetic mean. Median in cm, Sample standard deviation and Coefficient of variation (CV).
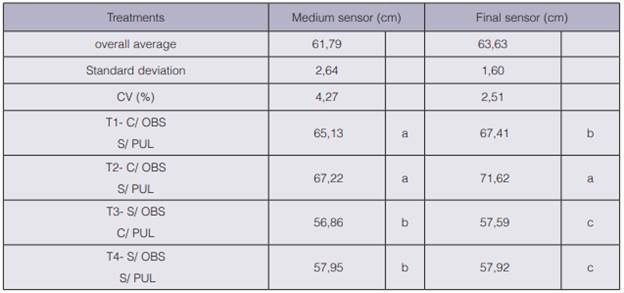
Equal and lowercase letters in the columns do not differ from each other by the Tukey test at 5% probability.
Figure 1 and 2 shows the characteristics of the spray bar for the treatments, where the sprayer is moved in a path with the obstacle. In the pitch with obstacle, the larger bar scale compared to the unobstructed treatment, and with respect to a spraying, no significant variation, with or without spraying during the trajectory, bar sensors.
The behavior of the sprayer bar, for treatments where the set traveled on a flat (dirt road) surface, without obstacle are in figures 3 and 4, and it is observed that for the vertical oscillations, under these conditions presented lower In this case, there was no significant difference with the use of spraying, Simove showed no limitations, with this practice during all treatments.
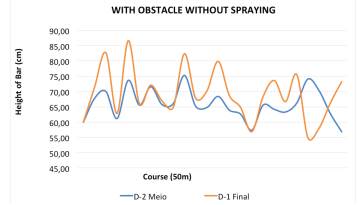
Figure 1 Oscillations of the bar with obstacle and without spraying, in order to represent the end of the spray bar, the two vertical ones during the course.
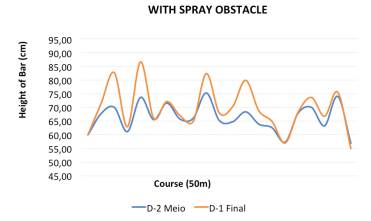
Figure 2 Oscillations of the bar with obstacle and spray, with (blue lines), represents the sensor in the middle of the bar and (orange lines) represents the final sensor of the sprayer bar, both consider the vertical movements during the course.
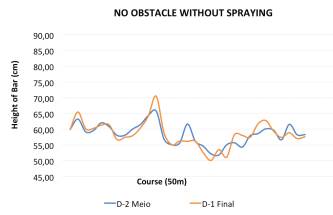
Figure 3 Oscillations of the bar under flat surface without obstacle and without spraying, with (blue lines), represents the sensor in the middle of the bar and (orange lines) represents final sensor of the sprayer bar, both consider the vertical movements during the route
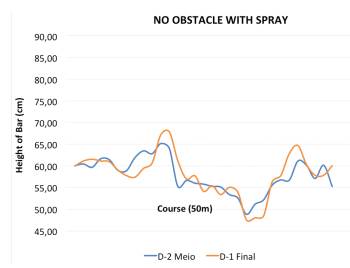
Figure 4 Oscillations of the bar under flat surface without obstacle and with spray, with (blue lines), represents the sensor in the middle of the bar and (orange lines) represents final sensor of the sprayer bar, both consider the vertical movements during the course.
Analyzing the interaction between the conditions of the treatments and the working conditions of the sprayer bar with and without obstacles, and with and without spraying, it was observed that there was no significant difference between treatments T1 and T4 in grating the height of the bar in ( cm).
In the middle sensor of the bar, the ones that fit in the same class statistically were also the T1 and T2, as they presented less vertical oscillations during the course. In the same treatment, there was a difference in the statistical class in the sensor at the end of the bar, because it has a larger amplitude because it is positioned at the end of the bar.
Thus, the practice of spraying in uneven terrain has greater movements of the sprayer bars, thus harming the overlap and uniform distribution of the spray, according to the example of figure 4.
However, the treatments T2 and T3 presented the results in flat terrain, the variation of the amplitude was smaller when compared with the amplitude obtained in the conditions with obstacle. With this, in the spraying performed on flatter surfaces, there is less vertical movement of the bar, thus increasing the quality and efficiency of the application.
The data of the bar height sensors were described in Simove’s display, so that the operator knows the height of the bars, instantaneously and constantly, and can even adjust the bar manually, for greater efficiency of the application.
During the conduction of all treatments, temperature (C °) and relative humidity (%) were collected through the respective sensors present in the system, in which all the data were shown in Simove’s display. ideal climatic conditions, constantly for greater efficiency of the application. They can determine the exact moment of spray application or stopping.
It is noteworthy that the climatic conditions of temperature and relative humidity collected did not influence Simove’s efficiency.
Conclusion
The use of SIMOVE was efficient for the use during work, being possible to carry out the readings of the vertical oscillations of the bar, temperature and relative humidity in a fast, efficient way.
In all tests, the results of the readings were similar within each treatment, making it clear that the readings are reliable.
The greatest variations of bar oscillation were shown in the treatments with obstacles.