Introduction
The introduction of alternative and clean energy technologies is urgent, in order to face energy security concerns, as well as fossil fuels depletion and their environmental impact. A possible solution is the use of hydrogen to enrich fuels in internal combustion engines (ICE) within vehicles or thermal plants, taking into account all its developing implications. The idea is to introduce a percentage of hydrogen to the motor and improve the engine’s behavior. Different authors point that the use of a fraction of hydrogen in the fuel blend increases the efficiency and decreases gas emissions into the environment. In (1) Wall cited that studies have shown a reduction of the hydrocarbon by adding hydrogen into the fuel in percentages as low as 5-10%, “the theory behind this concept is that the addition of hydrogen can extend the lean operation limit, improve the lean-burn ability, and decrease burning time duration”.
In addition, (2) noticed a 27.5% thermal efficiency improvement, carbon monoxide emissions reduction (approximately 25%) and higher levels of nitric oxides when using timing port injection and diesel/hydrogen mixtures instead of diesel/air.
Other works report computational and experimental results of using diesel/hydrogen as a dual fuel. With levels of 10 to 80% of hydrogen “the pressure increases at high compression ratios due to the high flammability and rate of hydrogen combustion. Moreover, hydrogen has a major flame velocity at stoichiometric conditions, which makes the engine getting closer to the thermodynamically ideal engine” (3).
Complementary to engine combustion cycles, other research areas have been focused on materials used in engine manufacture, in order to prevent its embrittlement and observe its reliability when exposed to a fossil fuel and hydrogen mix. The following is a review showing a number of aspects related to hydrogen embrittlement.
Embrittlement of ICE materials
Common ICEs running on hydrocarbon fuels are made of aluminum or ferrous alloys, like structural steels, stainless steels and sintered metals. Each metal piece in the ICE assembly has a different composition according to the pressure and temperature conditions of its operation. Table 1 shows some of the common ICE’s parts and its composition, for further details refer to (4).
Companies like Ford, Hyundai, General Motors, Honda and Chrysler have presented experimental and commercial vehicle lines including ICEs running on just hydrogen or hydrogen mixes. Improvements have been made in some components and in the system to withstand its use with hydrogen.
Table 1 Typical metal composition of ICE parts. Source: adapted from (4).
Part name | Material |
Cylinder block | Gray cast iron, compact graphite cast iron, cast Al alloy |
Piston | Al-Si-Cu-Mg alloy |
Piston ring | Gray cast iron, spheroidized graphite cast iron, alloy cast iron, spring steel and stainless steel |
Camshaft | Chilled cast iron, Cr-Mo steel, iron base sintered metal |
Valve | Heat-resistive steel, Ti alloy, SiC ceramics |
Valve seat | Iron base sintered metal, cast iron |
Turbo charger | Ni resist cast iron, cast stainless steel, super alloy |
Plain bearing | Al-Si-Sn and Cu-Pb alloys |
Specifically, Ford Motor Company proposed using shuttle bus E-450 with a “H2ICE” hydrogen motor, which was built with aluminum, aluminum alloys, stainless steel, forged steel and other materials (5). On the other hand, Mazda developed a Wankel rotatory engine running on hydrogen (6), which has a separated combustion and gas admission chambers inside. This ensures complete combustion while avoids abnormal behavior in the process.
In addition to ferrous and aluminum alloy materials used in this type of engine, ceramics have been utilized in engines, which allows the ICE to operate at “hotter temperatures (and thus more efficiently) and burn whatever fuel it is using more completely to reduce emissions” (7). Ceramics also work as thermal barrier and brings benefits such as lubricity and reduction of the heat losses.
Therefore, the materials used to manufacture engines depend on the operation conditions, and risks may be taken into account since materials could be exposed to hydrogen embrittlement. For example, (8) cited that steel is susceptible to hydrogen effect, above 493 K the gas will introduce in the metal interstices and react with the cementite (Fe3C), producing methane that will reduce steel strength and cracks will appear in the material. (8, p. 26) also points that “metals with high ductility at low temperatures are preferred to be used with liquid hydrogen. For example: aluminum, cooper, bronze and Monel, Inconel, titanium and austenitic stainless steel” (translated from Spanish). In general, non-porous materials are used to avoid hydrogen permeability.
In addition, NASA’s Glenn Research Center in its security manual emphasizes that embrittlement could be reduced by using alloys, particularly aluminum ones (9).
Classification of hydrogen embrittlement
Many classifications of hydrogen deterioration can be found. The most general ones divide embrittlement in two groups: i) internal and ii) external. The first one relates to the embrittlement caused by hydrogen contained in the metal matrix, as a result of manufacturing process; the second one is caused by exposure to hydrogen, which inserts inside the metal and modifies its mechanical properties.
In (10) deterioration of materials due to hydrogen is classified broadly as:
Templed martensitic embrittlement (TME) or hydrogen induced cracking (HIC), as a result of four factors: a) hydrogen presence, b) tensile strength, c) sensible microstructure (martensite) and d) temperatures below 200°C.
Hydrogen embrittlement (HE), divided into three types: a) HE as a consequence of the hydrogen generation on the surface, b) HE due to the presence of material in an atmosphere of this element and c) Internal HE.
Stress corrosion cracking (SCC), fracture by pressure and corrosion, three factors must be present: a) pressure, b) corrosion and c) higher temperatures.
NASA’s Office of Safety and Mission Assurance proposes a classification with three types of embrittlement: i) environmental HE, ii) internal HE and iii) hydrogen reaction embrittlement (11). In the first type of embrittlement (environmental HE), the hydrogen source is gaseous hydrogen, typical conditions promoting this HE are pressures from 10-6 Pa to 10-8 Pa and temperatures ranging from -100 °C to 700 °C, gas purity is important in this case. The cracking initiates on the surface or inside the material. Several methods have been used to analyze this type of HE, for example, notched and unnotched tensile, creep rupture, fatigue testing, fracture toughness and disk pressure tests. Also, the rate of embrittlement is performed by two processes, adsorption and hydrogen diffusion stage to the interstices (absorption), what actually promotes embrittlement.
The second type of embrittlement (internal HE) occurs at manufacturing process, electrolysis or corrosion of the materials, the typical conditions for this HE are H2 content from 0.1 ppm to 10 ppm and temperatures from -100 °C to 100 °C. In this type of embrittlement, the strain rate is important. Cracking initiates due to internal cracking, incubation, slow growth or fast fracture. Notched tensile delayed failure, slow strain rate tensile, bend tests, C-ring and torqued bolts have been used as methods for HE detection. Embrittlement speed can be controlled by the diffusion between different crystal layers.
The last type of embrittlement (by hydrogen reaction) is caused by gaseous or atomic hydrogen, this phenomenon has been observed within high temperature heat treatments, causing the generation of flakes or bubbles internally in the material. The metallographic visual observation or specialized equipment is the normally used testing technique. Since embrittlement is obtained from a chemical reaction in which hydrogen gas or hydrides are formed, an expansion occurs and material volume increases.
Stages of hydrogen insertion in metals
The following are the stages through which hydrogen inserts in some metals.
Adsorption: surface imperfections benefit hydrogen atoms induction and work like a trap immobilizing the atoms. When a series of defects in a line are part of the surface (grain joints), there is also an attraction of the hydrogen atoms. The mechanisms through which hydrogen adsorption is present are: a) electrochemical charge, b) atmosphere loads of hydrogen gas and c) surface conditions’ influence on the adsorption (presence of S2-, HS-, H2S).
Hydrogen absorption: is the step after adsorption (surface), some or all molecules can move through the metal interstices and this increases when higher temperatures or pressures are present (see figure 1), which increases the kinetic energy and mobilization of atoms into the metal matrix
The absorption tendency is described by the following equation, known as Fick’s Law:
(1)
Where D0 is the diffusion constant, Ea is the activation energy, T is the temperature of the metal, k is Boltzmann’s constant. Notice that, when increasing temperature, the ratio (-Ea / kT) decreases and the exponential increases, resulting in an increment of D (diffusion coefficient).
Absorption can be explained in two ways: the classical mechanism of absorption in a molecular form (12) and the currently proposed Crolet’s ion uptake mechanism (13). Equations for classic mechanism absorption kinetics are:
(2)
(3)
Where iabs is the reaction’s rate, Kabs is the absoprtion rate, Kdes is the desorption rate, C0 the hydrogen concentration in the metallic layer and (1- ) is the concentration in the active sites on the surface. The first factor refers to the absorbed elements and the second one is about desorption. As long as the first one increases and the second one decreases, the overall rate of absorption tends to increase.
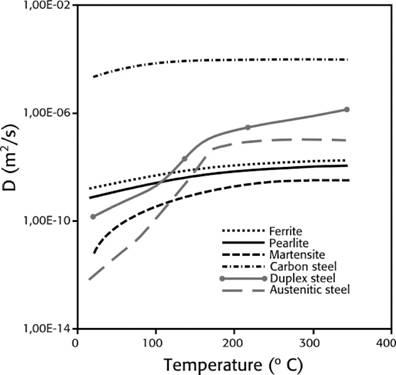
Source: own compilation based on data from (13), (33) and (34).
Figure 1 Hydrogen diffusion coefficient as a temperature function in different types of metals
About Crolet’s proposed absorption mechanism, it states that the protons transference can happen not only from water, but also from the deprotonation of molecules (kinetics are not detailed).
(4)
Atomic exchange: is another mechanism for insertion of the atoms on the surface, hydrogen atoms substitute metal’s atoms, increasing the embrittlement of the material. The mobility of one layer over the other decreases, resulting in crystal deformations due to the exchange of atoms with different characteristics.
If stress is applied, dislocations may appear in the material, this plastic deformation is known as Hydrogen Enhanced Localized Plasticity (HELP). The component used for the identification of deformations is the Burger’s vector (13, p. 61), which determines the slice’s magnitude and direction, forming a circuit known as Burger’s Circuit that works as delimiter of the dislocation area (14, p. 49). Figure 2 shows a sequence of the deformation mechanism in the material, specific examples of this deformation can be found in (15).
HELP deformation is observed in all types of metal and alloys systems: face centered cubic (FCC), body centered cubic (BCC), close packing (HCP), and precipitation strengthened alloys. Several authors have studied this type of embrittlement (16) - (19). It is shown that hydrogen enhances the embrittlement of metals, and, for example, the local flow-stress of iron could be reduced up to 50%.
Moreover, Shih, Robertson and Birnbaum (20) have observed that θ-titanium in presence of hydrogen promotes the movement of dislocations; later, Ferreira, Robertson and Birnbaum (21) showed the effect of hydrogen-enhanced mobility of dislocations in 310 S stainless steel and high purity aluminum.
Factors promoting insertion of hydrogen in metals
Chemical and physical factors should be examined when speaking about hydrogen insertion in metals, some of them are listed below.
Physical factors, due to changes of static conditions (e.g. hydrogen storage): plastic deformation of materials under high pressures have been observed, along with an increment of cracks as a consequence of ductility loss and high stress fracture increasing. For example, “in more or less ductile materials these high pressures deform the material and produce blisters of gaseous molecular hydrogen H2” (13, p. 36), then cracks are produced if the pressure exceeds a critical value. Specifically, for certain high yield strength steels used in hydrogen storage, cracks have been shown if pressures are increased from 10 MPa to 70 MPa (22).
Physical and chemical factors as a result of surface contact: the hydrogen molecule approaches too close to the metallic surface, then Van der Waals forces interact between both phases (gas and metal), there is also a chemical adsorption when valence forces interact. The molecule reaches an energy well, Ep, at a very close distance from the surface, in this point, H2 dissociation energy is exceeded by the chemisorption energy (Ech) and the molecule “can be cleaved into two individual atoms”. This interaction takes place at high temperatures when “sufficient thermal energy is available to increase the vibrational amplitude of both, the hydrogen atoms and those of the metal surface, and individual hydrogen atoms can reach and enter the metal surface” (23). Further reading about chemisorption refer to Christman (24), (25).
Chemical as a result of a reaction between hydrogen and the metallic surface: hydrogen reacts with an alloy or a contaminant contained in it, then hydrides are formed, reducing material’s ductility and stablishing a new phase inside the grain borders. Hydrides could be formed from reactions with Mg, Nb, Ta, Th, Ti, U, Zr and its corresponding alloys. The hydride phase has higher volume than the metallic phase causing plastic deformations in the material (26).
Chemical, as a result of electrochemical processes: it occurs specially in cells, galvanization, cathodic protection systems or surface oxidation. Hydrogen could be generated after reactions, and remains as part of a solution or inserted in the metal matrix. This processes usually promote mechanical weakening of the materials.
Case studies of HE on metals
Steel embrittlement. Steels are made mostly of iron and carbon, they are produced through an oxidation of the carbon and iron impurities. The simplest example of this reaction is:
(5)
Hydrogen will show cracks, especially within H2 pressures over 700 kPa and temperatures above 200ºC. Hydrogen inserts in the metal matrix, then, decarbonization takes place and the reaction liberates methane, cracks are shown when the gas is expelled. The damage of this process is irreversible for the mechanical piece. On the other hand, induced cracking occurs at room temperature without additional stress from the environment. Figure 3 shows a schematic sequence on how the fracture is formed in the material, (a) shows the adsorption of H2 when hydrogen is inside the metal and reacts; (b) then, the methane molecules press the matrix to get out to the surface and cracks are shown; (c) later, fracture is shown as a result of the embrittlement in the weakened cracked zones.
As reported in (27) alloyed steels with titanium oxide and aluminum oxide to prevent HE. Their study shows how titanium oxide and alumina molecules work as a reversible hydrogen trap, this phenomenon was demonstrated by observing the reduction of the hydrogen diffusion coefficient and the increment of its solubility inside the material. The use of this type of compounds enhances resistance to hydrogen in microalloyed steels.
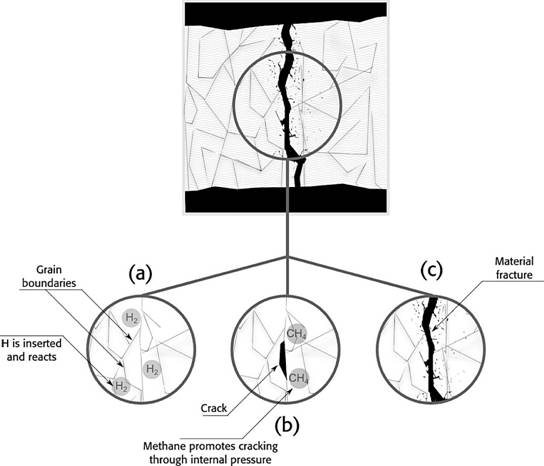
Figure 3 Fracture schematic sequence in a embrittled metal, (a) hydrogen inserts and reacts, (b) methane is expelled and small cracks are shown, (c) depending on mechanical stress, material will fracture around weakened areas.
San Marchi (28) mentioned that there is very little data about semi-austenitic stainless steels in gaseous hydrogen; “however, the available data indicates that the fracture resistance of semi-austenitic stainless steels is very sensitive to gaseous hydrogen”, then stated that these alloys “are not recommended for stress bearing components in hydrogen gas”.
Copper embrittlement. Copper alloys are generally embrittled when exposed to a hydrogen atmosphere, this is usual in welding processes. In this case the embrittlement is due to the chemical reaction when the copper oxide is reduced, that means
(6)
The physical result is observed at the material’s surface, where blisters, voids and holes appear after the hydrogen reacts, (29) associates it with the mechanism known as liquid metal embrittlement (LME).
Barthélémy (22, p. 17) mentioned that “Cu-Be was reported to perform well in the presence of hydrogen and have good mechanical properties”, however, also stablished that “for copper and its alloys it appears that more testing is necessary to completely understand the effects of hydrogen gas, particularly with regard to pressure”.
Aluminum embrittlement. Studies show that aluminum is highly resistive to HE in dry and gaseous environments. (30) have studied the AA7020 alloy (Al-Mg-Zn), specially developed for military and aerospatial applications. The alloy composition and grain structure determine the capacity of the material to stand against cracking and lamination. Under low levels of Zn and Mg (up to 4%, as in commercial alloys), hydrogen traps are produced, reducing gas accumulation and fracture risk.
Thermodynamically, aluminum has a low equilibrium solubility of hydrogen, but the surface oxide acts as a kinetic barrier to hydrogen insertion; however, “studies of hydrogen transport in aluminum are complicated by the low solubility of hydrogen, the kinetic effects associated with the native oxide and hydrogen trapping” (31).
Hardened steel embrittlement. (32) adapted a hydrogen injection system within a diesel engine. The use of hydrogen increased 14% the engine’s power peak, and a 43% efficiency was achieved compared to 28% of conventional efficiency (i.e. without hydrogen injection). Also, nitrogen oxides were reduced about 20%. The embrittlement was noticed especially on the nozzle needle tip, “because it works at 300 ºC and the speed of flow is high” (32, p. 6519).
In this test, injector’s needle and nozzle were manufactured with a hardened steel and the hydrogen inlet was covered with Teflon. Nitrile O-rings were used, nevertheless, no conclusions were determined about hydrogen effect over this material, it is well known that hydrogen deteriorates rubber pipes. To obtain a better injector’s dynamic response, Viton (vinylidene fluoride and hexafluoropropylene copolymer) O-rings and low inertia materials as titanium are recommended.
Prevention of accidents caused by HE in ICEs
Following, considerations and preventive solutions are presented when working within hydrogen environments.
Final designs assessment. Structures, welding types, joinnings, fuel flux and storage systems should be analyzed and verified with respect to existing legislation. It is also important to select materials according to a study that takes into account the hydrogen environment conditions to withstand.
Risk analysis and regulation adoption. Emergency procedures and risk assessment should be included to develop procedures in order to obtain fully adequate functionality and handling of hydrogen systems. For example, HAZOP technique could be applied (33).
Security equipment and monitoring. It refers to the use of congestion valves and alarm systems (hydrogen leak detectors). NASA emphasizes security requirements for hydrogen metal systems, further specifics could be found about materials in (9, p. 28), standard operational procedures (9, p. 34) and protection of personal and equipment (9, p. 42).
Conclusions
Mechanical properties of materials should be tested before developing a model of internal combustion engine using a fuel mix containing hydrogen or pure hydrogen.
Hydrogen embrittlement depends on hydrogen environment characteristics like pressure, temperature, and other factors like hydrogen adsorption/absorption properties of the material.
Hydrogen deteriorates a specific material through different mechanisms like stress corrosion cracking, hydrogen induced cracking or hydrogen embrittlement. All of them have to be avoided or diminished when choosing materials to manufacture internal combustion engines.
Procedure assessment for passengers’ safety is a paramount concern when using hydrogen in vehicles.