Introduction
Natural history collections represent invaluable heritage assets for museums and valuable resources for higher education research, and teaching programs. In prominent museums, such material is protected to study and preserve knowledge about specimens to manage discoveries under a safeguard process. Moreover, preserved natural heritage is of particular interest in academic contexts because it provides opportunities to use these collections as didactic resources to support theoretical courses and hands-on experiences with different specimens without extracting them from their natural habitats (Martini et al. 2022,).
The 3D modeling of skeleton collections has proven to be a powerful tool in higher education scenarios, offering access to realistic visualization of animals and fossils. The digitization of these materials has a significant impact on viewers as such representations are not commonly seen in everyday life. This can be a helpful tool to generate awareness about species’ anatomy. Additionally, studying animal skeletons provides valuable information and aids in the education of future natural sciences professionals. For instance, studying the anatomy of animal skeletons can help clinical disciplines better understand the species they treat and, thus, protect endangered species (Ye et al., 2023)
When natural science students study anatomy topics, examining skeletons can enhance their learning experience. Many students learn about wildlife through books. Since the images in the books are two-dimensional, students are unable to touch or see a 3D image of the structures they intend to learn about. Allowing these students access to natural collections that include bones can broaden their understanding of the anatomy of species (Cunningham, 2021).
Conservators employ different techniques to preserve these objects over time. In the preservation process, natural resins like paraffin wax, PVA emulsions, and PEG are commonly reported as materials used for consolidating waterlogged materials. Nonetheless, these invasive conservation processes have the potential to impact the results by modifying or damaging the specimen material due to the chemical features of the products used (Guareschi, Magni & Berry, 2023).
Environmental conditions also represent a factor capable of accelerating degradation through bioerosion processes, driven by exposure to light, oxygen, and chemical reactions associated with bone degradation (Caruso et al., 2018). The nonregulation of these three factors fosters adverse conditions such as the proliferation of bacterial communities and the growth of bacteria in bone material. Besides, these collections are handled and manipulated for educational purposes, and this can accelerate bacteria growth and additional damage (Eriksen et al., 2020).
Nowadays, with the increasing accessibility of digital fabrication techniques, new opportunities have emerged to preserve those assets using new methods. One such method is 3D scanning, where digitization based on photogrammetry technologies of natural heritage has been implemented as a preservation alternative. Three-dimensional modeling and photogrammetry protocols have proven to be valuable resources for conservators, allowing for the creation of digital 3D assets that can be stored in databases or repositories. These methods provide a detailed view and more accurate morphological preservation with less invasive procedures for the samples. They also offer a long-term solution to preserve these materials with educational manipulation purposes by 3D printing the digital assets in more durable and resistant polymers (Barreau et al., 2022).
Photogrammetric processing underlies numerous computer vision technologies such as surface scanners, laser scanners, or smart cameras for data acquisition through the application of image processing algorithms. The complementation of hardware and software capabilities solution has led to automated data acquisition processes adjusting phenomena such as refraction and reflection that create changes in dispersion and angles that lead to a chromatic image triangulating with different angles (Waltenberger et. al., 2021).
In addition, photogrammetry allows the user to perform measurements achieving high resolutions by creating points that are defined in an equation to refer to a focal length, aperture, object-in-focus distance, depth of field, and calibration in a controlled environment. The image acquisition process is a light beam triangulation method with a matrix image sensor that generates a plane of light that forms a scanning process with software for data processing on a mesh (Luhmann et al., 2013).
Considering the above statements about the utility of photogrammetry-based methods, 3D scanning with visible light provides an alternative to preserve that sample with high scientific and conservation value. This report documents the digitization process of natural heritage skulls from a zoology university museum and a wildlife rescue center facility. The aim is to test and establish the required protocols for image acquisition and processing for preservation, training, and outreach purposes harnessing the hardware and software utilities available in a digital fabrication lab. The whole methods and results described expose the lessons learned until now to offer this as a service of interest for organizations managing natural heritage.
Methodology
Some of the animal bones used for the essays described below were preserved, while others were prepared for scanning to be utilized in outreach and environmental education activities. The scanned samples consisted of selected parts from a collection of skulls, considering specific shapes that could be a challenge for the 3D scanner.
The following describes the workflow for transforming a sample into a digitized 3D model useful for training and outreach scenarios through virtual reality or 3D printed models. Some of the samples used for this project came from a rescue center, where the following process was employed to clean and bleach the bones.
Osteological Preservation
The use of safety equipment such as goggles, gloves, and masks, was mandatory to avoid exposure to dangerous bacteria and chemicals throughout the entire process.
After performing a necropsy to determine the cause of the death, the animal’s skull was removed from the body. Muscular tissue and accessory organs were then separated from the carcass as thoroughly as possible. The skull was initially buried in a perforated bag and placed in a location inaccessible to animals that might dig the sample out.
The duration for which the sample remained buried depended on the type and size of the animal. For instance, large birds (weighing more than 1kg) were retrieved from the soil after 3 weeks, while smaller birds were processed after 2 weeks. For adult mammal skulls (depending on the species), the samples were buried for an average time of a month.
The sample was macerated in hot water with soap, remaining in this solution for at least two weeks to ensure the complete saponification of fats, the acceleration of protein degradation, and the increase in the speed of the rotting process, allowing the easy removal of any organic material.
In the final step of this process, the bones were bleached, and any residual tissue or organic trace in the sample was removed. To achieve this, the skull was placed in a solution of water and sodium hypochlorite at a 1 to 10 ratio; the 3% solutions available for home cleaning were sufficient for this purpose.
The time that the sample remained in this solution depended on the fragility of the specimen. The skull was checked every ten minutes to prevent degradation or porosity in the bones. Once all organic matter was removed and the bones were fully bleached, the skull was removed from the solution and rinsed with enough water to remove the sodium hypochlorite and halt the chemical reactions induced by the previous steps.
To complete the bleaching process, the piece was immersed in a hydrogen peroxide solution with water at a 1 to 10 ratio. In this case, the time in which the object remained in the solution depended on the thickness of the bones. Finally, the skull was thoroughly rinsed to stop any further degradation caused by this solution, and the sample was left to dry in the sun for 24 hours.
Acquisition and Postprocessing of 3D Mesh
After the selection or receipt of a sample in the digital fabrication lab, the process consisted of two main steps and others that could be considered optional depending on the purpose of the final product. The process was conducted through the following steps. The sample was scanned in a darkroom. This step required previous calibrating and adjusting of hardware acquisition parameters based on the 3D scanning technology used. For this study, the Go!SCAN SPARKTM (Creaform, Canada), a portable 3D scanner with 0.050 mm accuracy and a 99-line white light system, was employed for target acquisition. A description of the equipment setup for image acquisition is shown in Figure 1.
For organic geometries, such as the organic specimens analyzed in this study, the samples were scanned from different orientations, generating two or more separated meshes that were merged by matching geometrical features. For mesh acquisition and optimization, two computational tools from the VXelements (Creaform, Canada) software package were used.
After merging partial meshes, small, isolated artifacts were generated, because this could cause light noise; they were removed with basic editing tools. This gross merged mesh was transferred through different packages for postprocessing of the 3D model. Depending on the purpose of the essay, several options were used to prepare and optimize the new digital asset. The mesh could be optimized for digital fabrication by 3D printing or CNC milling for mold casting, inspected using 3D metrology, or adapted and exported for virtual or augmented reality visualization in online platforms.
In both cases, visualizing or digital fabrication purposes, modeling tools allowed for filling holes by creating hollow structures or modifying textures. This process also facilitated the generation of new parts in the model based on the object’s symmetry. This service was applied for restoring a piece or designing new components from the scanned specimen. Inspection tools were used to measure the similarity between meshes and geometric entities, assign planes, and export that data to be modified in CAD software.
Manufacturing Processes and Quality Assurance
The general principles, fundamentals, and terminology related to additive manufacturing are defined by the ISO/ASTM 52900 standard. Several studies have reviewed its process categories, as new technological innovations and commercial solutions have emerged. In this study, three different 3D printing methods, related to these process categories, were used to fabricate physical replicas of the digitized assets, namely Fused Deposition Modeling (FDM), Stereolithography (SLA), and PolyJet.
Fused Deposition Modeling (FDM) is a method founded on the principles of thermal energy, surface chemistry, and layer engineering. In this method, a filament is heated to a semi-liquid state and extruded through a nozzle following the parameters of a 3D CAD model. Very precise thin beads of material are continuously deposited layer by layer, while the thermoplastic solidifies to form the final piece (Reddy, Davuluri & Boyina 2020). The FDM machine used in this study employed a 1.75mm filament diameter, and its dual extrusion allowed for the use of water-soluble support materials. This feature was useful to maintain the integrity of complex model structures, such as the skulls used in the experiments.
Stereolithography (SLA) is a high-resolution projection method based on the polymerization of liquid photosensitive resins. A computer-controlled UV laser moves beneath the liquid resin tank, enabling the formation of covalent bonds between the adjacent photocurable polymers to create a 2D pattern. Layer by layer, this process creates the final 3D model (Reddy, Davuluri & Boyina 2020). Prints generated using this technology often bring better surface textures and structural resolution. The SLA system used in this study required the piece to undergo postprocessing, involving washing with a solvent and curing with UV light, to achieve the mechanical properties of the selected material.
PolyJet technology uses printing heads equipped with multiple microscopic channels to simultaneously extrude two or more liquid resins of different colors or mechanical properties. This technology enables the printing of support materials, such as gel or wax, which can be removed with water or sandblasting after the printing without deforming the model. As these systems can print layers under 20 μm thickness, they can produce smooth objects with very complex geometries without deformation. Since jetted ink must be used, non-Newtonian fluids are required, imposing restrictions on materials selection; more complex requirements must be accounted for, such as ink viscosity, which can be managed by heating the print heads or adding reactive diluent additives in resins formulations (Vladinovskis, 2020).
If the purpose of digitization is to fabricate physical parts, 3D printing technology offers a solution capable of replicating organic structures, such as those examined in this study. At the time of the experiments, three 3D printing systems from technologies described above were available in the lab, and two specimen meshes were selected to test these systems. Each technology required the configuration of the print job using specific commercial software and involved different manufacturing process and timeframes. The FDM, stereolithography, and material jetting machines were tested for this purpose in the lab, employing specimens of significant natural heritage value.
To evaluate which technology was the best suited for this task, the same files were printed on three different machines. Figure 5 shows the results from a jaw scanned and printed with SLA, POLYJET, and FDM technologies.
From a qualitative perspective, all the techniques tested demonstrated promising results for replicating the specimens.
However, in each case, material-related conditions could affect the fabrication processes. For instance, in FDM, factors such as humidity in filaments, print core dimensions, or even the wall thickness of the model can affect high-fidelity replications. Similarly, in SLA and material jetting solutions, issues like resin compatibility and support removal can also affect the results.
The 3D metrology capabilities of certain 3D scanners, including the one used in this study, allow for the ability to measure a piece and have a quantitative notion of how closely the printed parts replicate the original scanned sample.
Considering the significance of accuracy in scientific and training scenarios, as well as the interests of the rescue center involved in this study-where veterinarian wildlife medicine interns can utilize replica models-a quantitative method to assess the fidelity of the replicas becomes crucial. A quality assurance test based on 3D metrology was implemented to compare the printed results with the original scan.
Visualization and Virtual Reality Tools
As 3D scanning technologies bring the chance to export files in several formats compatible with almost every 3D visualization and manipulation software, there are different solutions to be used for these purposes. Depending on the final users and scenarios, optimizing file sizes is useful to avoid long loading times for the model.
The models generated in this study are compatible with Microsoft applications such as 3D Paint or OneDrive cloud visualization tools. Furthermore, platforms that provide virtual reality visualizing options, namely Sketchfab, were tested. Sketchfab will be used to develop didactic tools for environmental education workshops at the rescue center.
Analysis and Results
The results from the acquisition and mesh processing were exported in several compatible file formats with the interest purposes of this study. The digitized models include real-scale dimensions of the objects and even textures, which can be saved within the 3D files or as separate bitmaps.
Samples between less than 10 centimeters (about 3.94 in) and at least 60 cm (about 1.97 ft) in length were successfully scanned. Some of them presented challenges for the automated setup of the scanning system, particularly complex structures inside craniums, very thin bones, or teeth that did not remain intact.
Despite this, the software platform used in this study contained the tools to repair missing structures of the cranium, such as teeth, by applying symmetry to create new mirrored replacements for absent parts. It was also able to import multiple meshes from a separate work session for assembly.
Figure 2 shows a crocodile cranium with significant deterioration, despite careful manipulation at the museum, and the results of the digitization process. This specimen was chosen for its size (approximately 53 cm, or 1.74 ft in length). Both the cranium and mandible were scanned and optimized separately, then aligned and fused to generate a unified mesh, enabling a more complete visualization of the entire cranium.
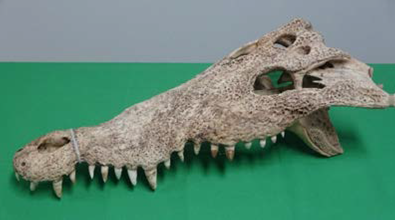
Note. Source: own study.
Figure 2 Crocodile (Crocodylus acutus) Cranium from the Zoology Museum Collection
According to Cunningham (2021), this type of digital asset can be useful in virtual learning scenarios because it can be manipulated with programs that allow for detailed observation of the structures in distinct positions, although an underlying problem is the weight of the mesh data.
Another advantage highlighted in the results was the clear identification of very complex morphological structures and anatomical details in this specimen, such as cranial foramina, which can be visible in the 3D model image shown in Figure 3.
This advance is significant for academia because it enables the enrichment of databases used for cranial geometric and morphometric analysis to further understand cryptic species facing diverse levels of anthropogenic threats. This type of digitization offers an opportunity to measure these processes (Carr et al., 2021).
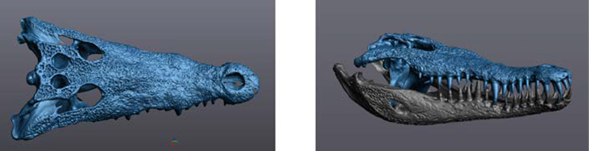
Note. Source: own study
Figure 3 Crocodile (Crocodylus acutus) Skull Mesh with Detected Cranial foramina and Complete Head Assembly
Understanding the placement of the diverse foramina and other smallscale structures of the skull can be highly beneficial in veterinary medicine, not only for surgical applications but also for understanding inflammatory processes within the braincase, identifying sites for common formation of abscesses, assessing areas of innervation, and determining anatomical placement of soft tissue structures. Additionally, this knowledge provides a baseline for what is considered normal, allowing for comparisons with potentially pathological specimens (Chen et al., 2017).
Texturing and color data can be features of particular interest for training and educational scenarios. Figure 4 shows a model of a dolphin cranium that includes texture data, where a whitish fungus is visible on the upper side of the cranium. This fungus can be removed from the file if a model for outreach or scientific demonstration purposes is required.
Although the manufacturing of high-fidelity replicas implies considering more complex features, such as bone density, which cannot be achieved by these techniques, according to Edelmers et al. (2022), the texture provides significant data from anatomical structures and complexity, which can be useful depending on final users.
If the models are to be printed as teaching resources, some of the digitized samples have already been printed using three different 3D printing technologies. Figure 5 shows a jaguarundi jaw (Herpailurus yagouaroundi) printed using FDM, SLA, and material jetting.
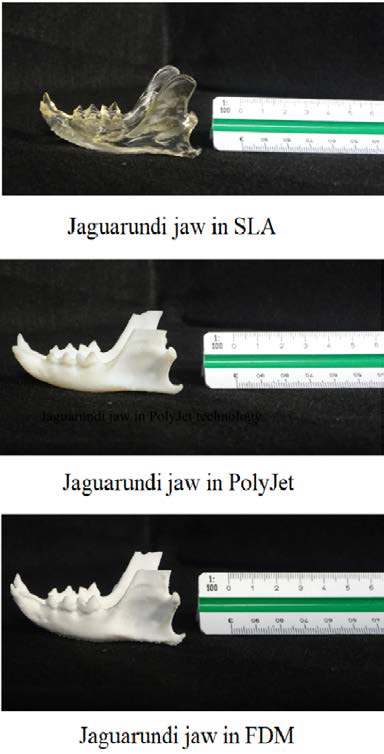
Source: own study.
Figure 5 Jaguarundi Jaws Printed Using Three Different 3D Printing Technologies Note.
A comparison between printed models and the original scan was conducted using 3D metrology and quality assurance protocols to obtain a quantitative reference for the replication of the samples. Figures 6 and 7 show the results of the assay for the same jaw model printed with three different materials. The analysis generated a color map where the green surfaces indicated a high fidelity or optimal standard deviation, while deviations toward warmer or cooler colors signified lower fidelity. These areas can be interpreted as parts or triangles added in the restoration of the model or as features missed during the manufacturing process.
As shown in the color map in Figure 6, SLA and PolyJet results provided the highest accuracy for this case. In another analysis, a sloth cranium scan was compared to a 3D printed model produced using an Objet 30 Prime (Stratasys USA) machine. The results displayed in Figure 8 include a color map illustrating the standard deviation set up for the test.
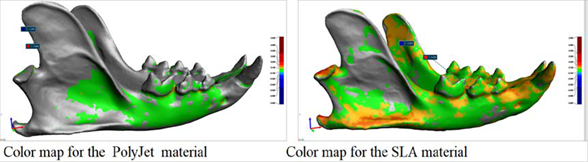
Note. Source: own study
Figure 6 Quality Assurance Results for the Same Jaw Model Printed Using Polyjet and SLA Technologies with Commercial Resins
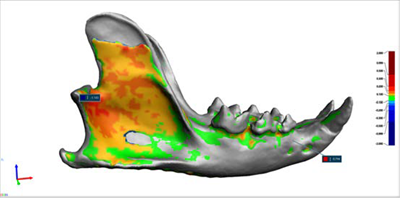
Note. Source: own study
Figure 7 Quality Assurance Results for the Same Jaw Model Printed Using the FDM Technology with ABS Material
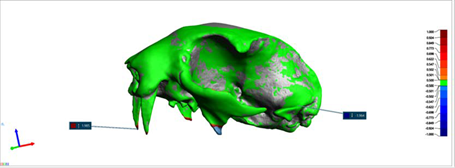
Note. Source: own study
Figure 8 Color Map from Quality Assurance Results of a Sloth’s (Choloepus Hoffmanni) Cranium Printed Using Polyjet Technology
In this case, the results indicate only two points with high standard deviation (1.985 mm) at the tip of the fangs, and one point with a lower standard deviation (-1,964 mm) at the base of the skull. These geometric differences correspond to specific areas reconstructed by software tools.
Aside from these two areas, the errors observed can be attributed to systemic or aleatory factors, such as the operator’s experience with the scanner, limitations of the optical system in accessing distant hollow parts, or even the mesh alignment performed using software tools (Garashchenko, Kogan & Rucki, 2022).
The educational potential of the combination of 3D imaging, modeling, visualization, and printing techniques to develop alternative and sustainable didactic resources for training in scientific disciplines has been widely demonstrated in higher education contexts.
Students in other natural science degree programs, such as zoology, ecology, paleontology, conservation biology, and wildlife forensics, among others, may benefit from printed models to have long-lasting educational assets. Considering that natural history collections in museums and universities are facing crisis due to factors such as lack of funding and researchers not depositing materials (Salvador & Cunha, 2020), it is imperative to find ways to ensure that future generations can access wildlife samples that endure over time. Future students in science degree programs who need to examine such samples closely to better understand concepts of the morphology, anatomy, and physiology of the species they study may find that printed models offer one of the closest alternatives to real specimens. Considering that processes such as the examination and display of zoological specimens in museums and educational settings imply the removal of specimens from their natural environments, resulting in unsustainable practices that impact the well-being of the ecosystems worldwide, groups from specific areas, such as marine biology, have been motivated by the hypothesis that in public and academic settings there is a clear link between rarity and access limitations to certain specimens. These limitations lead to a decrease in hands-on education and research capability to document the digitization process and replica fabrication of natural heritage for use in educational scenarios (Keaveney et al., 2016).
The same issue can be extrapolated to tropical biology, zoology practices, or veterinary medicine focused on tropical species. In these fields, students’ hands-on experience requires access to fresh corpses each academic cycle to be prepared to handle real-life cases after they complete their degrees.
Other hands-on scientific disciplines, such as those related to human health, have widely documented and highlighted the contributions of implementing scanning techniques like X-ray CT or MRI, combined with 3D printing and visualization, to train interns and specialists on their academic formation and even during their professional practices. These techniques improve presurgical planning, decision-making, and handling of tailored clinical needs.
For instance, Kudryavtseva et al. (2020) support that modern trends in medical education, both in general and specialized fields, are related to the introduction of visual teaching aids in the training of students, residents, and medical practitioners where 3D printing represents one of the most promising directions to solve the problem, in addition to pointing out the creation of collections of normal and pathological body parts to support the educational process.
3D-printed bio models provide anatomical models that allow teachers to develop practical workshops and create educational experiences based on visual assistance strategies (Altwal et al., 2021; da Silveira et al., 2021; Ye et al., 2023).
Recent advances in human medicine have been used to teach anatomy, prepare for surgery of the cranium, or even allow for the practice of certain medical procedures (Chan et al., 2015) This could easily be translated into use for the veterinary field as well, allowing for future medical professionals to have a three-dimensional understanding of their object of study, understanding how soft tissue fits over an osteological framework and allowing for students to practice on the material without worrying about harming potentially priceless biological specimens.
Even though there are evident advantages to using 3D technologies for preserving natural heritage, and specifically its harness in both formal and non-formal educational experiences, there are disadvantages to address.
Some of them are related to energy consumption, as the process of melting materials with heat or laser requires significant electricity. Additionally, heated polymers generate toxic emissions, implicating an environmental cost. Another important limitation is the range of compatible printing materials. Other factors to consider include maintenance costs, facility upgrades, space constraints, raw materials costs, preand postprocessing equipment expenses, and software fees (Vladinovskis, 2020).
Fortunately, the proliferation of makerspaces around the world has demonstrated their role as places to contribute with stakeholders to create prototypes and concept tests for innovative ideas with the potential to become alternative educational resources or educational technology entrepreneurship. Previous projects, like this collaboration between a university makerspace, museums, and rescue centers, contribute to future decision-making and investments.
As an alternative for visualization purposes, some of the finished meshes were uploaded to the 3D viewer platform Sketchfab. This solution was selected because it provided the setup to visualize the models using low-cost VR lenses that work integrated with mobile phones. To achieve the uploading process, file sizes were optimized according to platform requirements. Figure 9 shows the results of a small and fragile bird cranium (approximately 86.690 mm or about 3.41 inches in length) with very delicate features, now preserved for digital manipulation. The platform enables visualizations on a laptop, desktop computer, or cell phone, with the option to switch to a stereoscopic view compatible with VR lenses. It also includes sharing options, allowing the use of an HTML code for embedding it in a virtual learning environment.
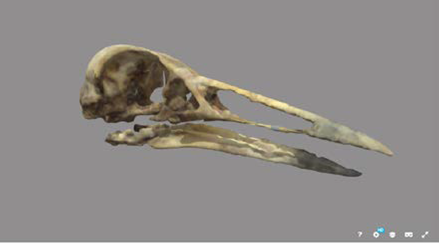
Note. Source: own studio https://skfb.ly/oKKN9
Figure 9 3D Model of a Grey-Necked Wood Rail (Aramides Cajaneus) Cranium Integrated into Sketchfab 3D Viewer for VR Visualization.
One of the contributions and main purposes of this work was to examine a solution to address the rescue center’s need to overcome current challenges and harness the synergy with the university makerspace to create and test new solutions in non-formal educational experiences, while avoiding the limitations related to access and management of digital fabrication technology.
The rescue center funds the operation through donations and educational tours of the sanctuary, where visitors learn about the rescued wildlife´s biology and practices to prevent wildlife from ending up in rescue centers. Real skulls, which deteriorate quickly due to repetitive manipulation are used to illustrate explanations about wildlife’s anatomy. Using the printed models, the rescue center may provide a better educational experience by allowing the visitors to touch and examine printed models. This approach aims to provide a more impactful environmental education experience that can foster a better attitude toward wildlife conservation (Ardoin et al., 2020).
Conclusions
The digitization processes based on photogrammetry and 3D scanning technologies provide a feasible solution for heritage preservation, particularly for the scientific and knowledge preservation of high-value biological samples that are susceptible to degradation due to environmental conditions.
Optical-based 3D printing solutions, such as SLA and material jetting, have demonstrated greater accuracy in replicating anatomical features, which is of interest for hands-on training scenarios in veterinary medicine.
The digital assets produced through these digitization processes can be harnessed for environmental education learning experiences that incorporate innovative trends and educational tools such as virtual reality manipulation and exploration of specimens by students without the risk of damaging high-value samples.
The combination of 3D imaging, modeling, and printing techniques presents the opportunity to develop more advanced skills, such as surgical practices, in hands-on experiences for health-related disciplines. It also supports the study of basic knowledge disciplines by access to more sustainable educational resources.
Digital assets and replicas contribute to the protection and preservation of ecosystems, avoiding the extraction of specimens and fresh corpses for educational and research practices. Other conservation organizations, including museums and rescue centers, could enhance their attention to the public by incorporating non-formal educational experiences to raise environmental awareness and local biodiversity knowledge. Digital fabrication labs and makerspaces, through synergies with external organizations such as museums and rescue centers, can prototype new educational products and services to current needs, while overcoming limitations related to digital fabrication technology management and commissioning.