1. Introduccion
Pineapple (Ananas comosus) is a perennial crop widely produced in tropical regions (1). Costa Rica is one of the most prominent producers. According to (2), during 2020, Costa Rican production of pineapple reached 2 600 000 metric tons for a cultivated area of 40 000 hectares.
Every two years, pineapple plants must be renovated to start a new production cycle, which produces around 250 tons of lignocellulosic material per hectare, mainly pineapple leaves (3); these residues must be treated before a new plantation. Current practices include natural decomposition, chemical and thermal burning, both non-environmentally friendly options. The decomposing material is susceptible to pest development which impacts nearby cattle and farming establishments (4); in addition, natural decomposition can take up to 13 months, reducing crop productivity. During the burning of crop residues, soil nutrient content is affected and there is an important effect on air pollution (5), while herbicide treatments, without dosing controls, may cause chemical leaching into nearby bodies of water as well as the destruction of the soil microbiome (6).
Off-site treatment requires the generation of high value-added products to compensate the transportation costs and make the process feasible. Pineapple leaves have a solid portion consisting primarily of cellulose, hemicellulose and lignin (around 56 % of total solids) (7), which is attractive for biofuel production applications. Some off-site treatments that have been studied in recent years include bioethanol production, composite materials, and biochar or activated carbon production.
Bioethanol production consists of the yeast anaerobic fermentation of sugars which requires mechanical extraction of pineapple leaves juice (7) or a hydrolytic and/or enzymatic pretreatment of the leaves to reduce long chain carbohydrates into fermentable sugars. Hydrolytic pretreatment can be performed in a basic medium, acidic medium or with hot water or steam (8) –( 1 1), and enzymatic pretreatment includes the use of cellulases (mainly endo-1,4-β-D-glucanase, exo-1,4-β-D-glucanase/exo-cellobiohydrolase and β-glucosidase) (12), (13). Although bioethanol is a suitable substitute for fossil fuels, there are several limitations along the production process which makes it crucial to generate new research strategies that improve process efficiency and economic costs (1). Some of these limitations include the low digestibility of biomass, carbohydrate degradation during pretreatments and use of toxic chemicals, energy, and water (2). Additionally, the fermentation broth requires a product separation process which generates additional inputs and a high-energy consumption.
Moreover, the use of pineapple fibers for biomaterials has been investigated for polymer composites for various applications (automotive, biomedical, food packaging, etc.) (14) – (16) and other engineering applications, such as construction materials (17), (18). The pineapple fibers and extracts provide an improvement for the mechanical properties, and their biodegradability is one of the most sought-after characteristics for eco-friendly solutions. These processes generally require previous drying steps, and the separation and size reduction of the fibrous material are energy intensive operations, as well as the use of toxic chemicals for the pretreatments. In any case, further studies are needed to simplify the processes and make them cost effective for the industrial applications to be feasible (18). Biochar and activated carbon are carbonaceous materials obtained by thermochemical conversions such as pyrolysis and torrefaction (19), (20) from sources such as pineapple waste. Their applications on soil remediation and water contaminants removal have been studied in recent years (21) – (23). The versatility of these materials, as well as the variety of by-products generated, make this alternative economically feasible in certain production conditions (24); however, the process is energy sensitive and depends on the characteristics of the biomass, as well as the method used for the conversion and the operation parameters selection (temperature, pressure and residence time) (25).
Other alternatives to use pineapple waste is the Aqueous-Phase Reforming for the production of hydrogen (26) and hydrothermal liquefaction of pineapple leaves to obtain biocrude (27). However, these alternatives are in a research-stage and require further studies to be implemented on an industrial scale (28). Another promising alternative to treat the residues and generate a high value added product is anaerobic digestion, which is a process that degrades organic materials in the absence of oxygen to produce biogas, a stable and high-energetic biofuel composed of methane and carbon dioxide for energy generation applications (29). This process has the advantage of treating organic residues in a liquid medium, removing the requirement of prior drying, which is fundamental since the material has high water content of around 85 % (30). To obtain this liquid medium, (7) applied a mechanical extraction of the pineapple leaves to obtain a juice containing 6,2 % of solids that consist of 72,5 % carbohydrates (7). The resulting digestate consists of a nutrient rich broth with fertilizer applications, with minimal further treatment required (31).
Furthermore, anaerobic digestion, being a microbial degradation process, requires control over certain parameters to ensure an efficient transformation of the residues. Some of these conditions include temperature, pH, volatile fatty acids, hydraulic retention time, and an appropriate carbon/nitrogen ratio (20-35:1 (C/N)) (32). Pineapple leaves can have a C/N ratio of up to 41:1 (30), while pineapple leave juice has 14 % of crude fiber, which means codigestion with a nitrogen rich substrate can be very beneficial. Studies show that codigestion of two or more substrates provides a synergistic effect reducing unfavorable conditions and increasing methane yield (33).Synergistic effects include an increase of bacterial diversity, which can speed up the hydrolysis rate and methane yields, the liberation of ammonia during protein degradation and fermentation, which, in combination with ammonium ions in aqueous solution, has a buffer effect maintaining pH values in an ideal range for anaerobic digestion and a nutritional enhancement in the media that promotes the reproduction and development of the anaerobic microbiome, while a balanced distribution of carbohydrates, proteins and lipids are considered to increase methane yields (34).
Previous studies show that pineapple production waste, including peel, cores, pulp, and leaves, can have the technical potential to generate biogas in a feasible process. During the study of the production of biogas in a plug flow reactor using pineapple pulp and peel, (35) determined that the increase of the concentration of pineapple by-products in the feed from 2 % at a hydraulic retention time of 7 days to 4 % at a hydraulic retention time of 10 days doubled the biogas production rate, which could be increased up to 52 % more by recirculating the fermentation effluent at 40 % (v/v). (36) determined that pineapple peel and core codigestion with cow manure resulted in the production of a biogas with more than 60 % methane. This study revealed that a mix proportion of 1:1,5 (manure:fruit waste) yielded a higher methane content and reduced the hydraulic retention time by 5 days (36). In the case of liquid by-products, (37) found that the anaerobic digestion of squeezed pineapple liquid wastes (extracted from solid wastes) in a hybrid reactor yielded up to 0,504 L/gCOD of biogas with 0,277 L/gCOD of methane. This study aims to implement an anaerobic digestion process able to treat pineapple waste in the North and Atlantic region of Costa Rica, in combination with chicken manure, to provide a feasible solution to farmers while high value-added products are generated. Anaerobic codigestion of pineapple leaves juice with chicken manure could result in an increase on methane production and a decrease in hydraulic retention time, compared to each substrate digested on its own (36), (38).
2. METHODOLOGY
2.1. Substrate and inoculum
Chicken manure and pineapple leaves were obtained from the northern production area of Costa Rica. The leaves were cleaned prior to the juice extraction; an industrial extraction mill was used to separate liquid and solid phases. The liquid portion was collected and sieved to remove coarse solids. Substrates were refrigerated at 6 °C prior their use. Stabilized sludge from an anaerobic wastewater treatment plant located in Moravia Costa Rica, (Latitude: 9.971; Longitude: -84.055) was used as the inoculum. This sludge was recovered with a pump from the tertiary treatment.
2.2. Biomethane potential tests
Biochemical methane potential tests were carried out in 200 mL serum bottles, with a 150 mL working volume, which contained 130 g of inoculum and enough substrate to reach an inoculum to substrate ratio of 2:1 (on VS basis), according to (39). Five different treatments were carried out, including the 3 substrate mixes (70/30, 80/20 and 90/10 for leaves juice and chicken manure, respectively) and each substrate on its own. A blank assay with only the inoculum was used to correct the methane potential of the inoculum. All runs were carried out in triplicate for a total of 18 samples. The working volume was adjusted by adding distilled water and each bottle was sealed with a rubber septum and a cap prior to flushing with nitrogen gas to displace oxygen in the head space. All samples were incubated at 37 °C with continuous stirring at 110 rpm for 30 days, monitoring gas production daily by volumetric measurement.
2.3. Analytical methods
Total solids, volatile solids and pH determination were carried out according to (40). Biogas was quantified volumetrically by direct measurement with graduated syringes. Volumes were normalized for standard temperature (273 K) and standard pressure (1 atm).
2.4. Techno-economic analysis
The scenario with more biogas productivity in the experimental section is used to run a technoeconomic analysis with a capital investment estimation, based on the delivered equipment cost for a fluid processing plant, according to the Peters and Timmerhaus methodology (41). The considered production process is shown in Fig. 1.
he leaves are collected and transported to the processing plant, where the juice is extracted mechanically. Chicken manure is also collected and transported to the processing plant. A mixed feed of juice and chicken manure enters the reactor for the codigestion process. The feed basis for the study was 250 tons of leaves per day (corresponding to 730 hectares farm). The anaerobic digestion reactor operates at 37 °C, with continuous stirring at 110 rpm, for a hydraulic retention time of 15 days.
Capital investment was calculated adding direct and indirect costs. These calculations were based on percentual estimates recommended by (41) for a fluid processing plant, using the delivered equipment cost as basis. Equipment cost consists on the cost of the extractor, obtained from (4 2), while the cost for the anaerobic reactor was estimated using the Aspen Process Economic Analyzer (APEA) included in the software Aspen Plus V11. For this simulation, the composition of the feeds used is shown in TABLE I.
TABLE I PINEAPPLE LEAVES JUICE AND CHICKEN MANURE COMPOSITIONS USED IN THE SIMULATION
Compound | Pineapple leavejuice (%) (7) | Chicken Manure (%) (43) |
Hemicellulose | - | 0,1815 |
Lignin | - | 0,0361 |
Xylose | 0,0160 | - |
Glucose | 0,0106 | 0,0385 |
Protein | 0,0087 | 0,1543 |
Fats | 0,0022 | 0,0156 |
Water | 0,9380 | 0,2981 |
Ammonia | - | 0,0024 |
Lactic acid | - | 0,0051 |
Acetic acid | - | 0,0067 |
Propionic acid | - | 0,0003 |
Butyric acid | - | 0,0012 |
Other carbohydrates | 0,0184 | - |
Inert | 0,0062 | 0,2602 |
The anaerobic digestion reactor was simulated as a stoichiometric reactor, with a hydraulic retention time of 15 days. The hydrolytic reactions were included according to the method presented by (44), and the reactions adjusted to the components present in the system (TABLE II).
TABLE II HYDROLYTIC REACTIONS OCCURRING IN THE ANAEROBIC DIGESTOR
Compound | Reaction | Conversion |
Hemicellulose | C5H8O4 + H2O → 2,5 C2H4O2 C5H8O4 + H2O → C5H10O5 | 0,7 |
0,6 | ||
Xylose | C5H10O5 → C5H4O2 + 3 H2O | 0,6 |
Glucose | C6H12O6 → 2 C2H6O + 2 CO2 | 0,5 |
Ethanol | 2 C2H6O + CO2 → 2 C2H4O2 + CH4 | 0,7 |
Protein | C13H25O7N3S + 6 H2O → 6,5 CO2 + 6,5 CH4 + 3 H3N + H2S | 0,7 |
Triolein | C57H104O6 + 3 H2O → C3H8O3 + 3 C18H34O2 | 0,7 |
The acidogenic, acetogenic and methanogenic reactions are presented in TABLE III. Fractional conversions were assumed to adjust the biogas product as close as possible to the experimental yield. All thermodynamic properties were calculated with the NRTL model, adjusting missing parameters with UNIFAC model.
TABLE III ACIDOGENIC, ACETOGENIC AND METHANOGENIC REACTIONS OCCURRING IN THE ANAEROBIC DIGESTOR
Compound | Reaction | Conversion |
Acidogenic Phase | ||
Glucose | C6H12O6 + 0.11 H3N → 0,11 C5H7NO2 + 0,74 C2H4O2 + 0,50 C3H6O2 + 0,44 C4H8O2 + 0,69 CO2 + 1,03 H2O | 0,5 |
Glycerol | C3H8O3 + 0,04 H3N + 0,03 CO2 + 0,0005 H2 → 0,04 C5H7NO2 + 0,94 C3H6O2 + 1,09 H2O | 0,5 |
Acetogenic Phase | ||
Oleic Acid | C18H34O2 + 15,23 H2O + 0,25 CO2 + 0,17 H3N → 0,17 C5H7NO2 + 8,70 C2H4O2 + 14,50 H2 | 0,5 |
Propionic Acid | C3H6O2 + 0,06 H3N + 0,31 H2O → 0,06C5H7NO2 + 0,93 C2H4O2+ 0,66 CH4 + 0,16 CO2 + 0,0006 H2 | 0,9 |
Methanogenic Phase | ||
Acetic Acid | C2H4O2 + 0,02 H3N → 0,02 C5H7NO2 + 0,95 CH4 + 0,07 H2O + 0,95 CO2 | 0,9 |
Hydrogen | 14,50 H2 + 3,83 CO2 + 0,08 H3N → 0,08 C5H7NO2 + 3,42 CH4 + 7,50 H2O | 0,9 |
Operating costs include labor, raw materials, utilities, and maintenance. Labor costs were based on the local minimum salaries with an added 20 %, considering a labor burden of 90 % based on the current local rate. Raw material cost consist of recollection and transport costs calculated according to (42), adjusting diesel cost in Costa Rica to 1,33 US$ /L. Utilities consist of electricity cost for heating and stirring the reactors, estimated with the APEA tool, as well as operating pumps and extractor, which were calculated from the energy balance, considering that the electricity cost in Costa Rica is 0,15 US$/kWh. Maintenance costs were estimated as 5 % of the total capital investment according to (41). The revenues for biogas were considered as 0,50 US$/kg, adjusting local LPG cost proportionally with the heating value of each fuel. On all cases, it is considered that the plant operates 360 days per year.
3. RESULTS AND DISCUSSION
3.1. Biomass characterization and biogas production
The biomass characterization is shown in TABLE IV. Characterization data is used to reach an inoculum to substrate ratio of 2:1 (on VS basis) for the biomethane potential test.
TABLE IV CHARACTERISTICS OF SUBSTRATES AND INOCULUM USED FOR ANAEROBIC CO-DIGESTION
Sample | Moisture Content, MC (%) | Total Solids, TS (%) | Volatile Solids, VS (%) | VS/TS (%) |
Inoculum | 99,19 | 0,81 | 0,43 | 53,19 |
Pineapple leaves juice | 95,28 | 4,72 | 3,81 | 80,72 |
Chicken Manure | 34,36 | 65,64 | 52,03 | 79,27 |
Chicken manure was added to generate 3 substrate mixes as shown in TABLE V. Due to its high content on total solids, this addition resulted in an increment on the VS concentration, compared to the original substrate (100 % pineapple leaves juice). On TABLE VI is presented the pre-digestion and post-digestion characterization of the BMP reactors.
TABLE V MIXING PROPORTIONS USED FOR ANAEROBIC CO-DIGESTION
Mix | Pineapple leaves juice (%) | Chicken manure (%) | Theorical VS (%) |
1 | 70 | 30 | 18,28 |
2 | 80 | 20 | 13,46 |
3 | 90 | 10 | 8,63 |
TABLE VI PRE-DIGESTION AND POST-DIGESTION CHARACTERIZATION OF CULTURES EVALUATED IN BMP TEST
Pilot Reactor | pHpreA | pHpost | TSpre (%) | TSpost (%) | VSpre (%) | VSpost (%) |
Inoculum | 8,0 ± 0,15 | 8,2 ± 0,27 | 0,2 ± 0,17 | 0,1 ± 0,01 | 0,2 ± 0,05 | 0,1 ± 0,09 |
Chicken Manure | 8,2 ± 0,04 | 8,1 ± 0,09 | 0,2 ± 0,06 | 0,2 ± 0,01 | 0,2 ± 0,03 | 0,0 ± 0,01 |
Pineapple leave juice | 7,6 ± 0,06 | 7,8 ± 0,03 | 0,2 ± 0,20 | 0,2 ± 0,00 | 0,2 ± 0,08 | 0,1 ± 0,01 |
Mix 1 | 8,1 ± 0,06 | 7,9 ± 0,08 | 0,2 ± 0,03 | 0,2 ± 0,01 | 0,2 ± 0,02 | 0,0 ± 0,00 |
Mix 2 | 8,2 ± 0,04 | 7,8 ± 0,02 | 0,2 ± 0,02 | 0,2 ± 0,01 | 0,2 ± 0,00 | 0,0 ± 0,00 |
Mix 3 | 8,1 ± 0,04 | 7,8 ± 0,06 | 0,2 ± 0,02 | 0,2 ± 0,01 | 0,2 ± 0,01 | 0,0 ± 0,01 |
A: The pH of cultures was not adjusted.
Fig. 2 presents the methane production curves for the different studied systems. As expected, the inoculum and 100 % pineapple leaves juice produce the least amount of biogas. However, the 100 % chicken manure samples present an irregular behavior. Biogas production starts out high and then there is a lag period of almost 300 hours, before the production continues growing. According to (45), lag periods have been observed in chicken manure anaerobic digestion due to high concentrations of Free Ammonia Nitrogen (FAN), which affect unacclimated bacteria. Another possibility that explains this behavior is an imbalance in acidogenic and methanogenic bacteria causing a high production of volatile fatty acids which result in a lower pH that reduce the methane production during this lag period (46). These results coincided with the results presented by (47). The reactors with chicken manure reduced their pH, due probably to higher VFA production. This behavior is typical in successful anaerobic digestion processes. This change in pH was not observed on the pineapple leave juice reactors. These reactors increased their pH (0,13 on average). Also, is possible to observe that the VS consumption is higher in the co-digestion reactors (68 % VS reduction on average) in comparison with the reactors fed with the chicken manure (31 %) or the pineapple leave juice (66 %).
Results also show that between 400 and 600 hours, samples containing pineapple leave juice achieve a faster hydrolysis. These results are to be expected since according to (48), bromelain enzymes are present in all parts of the pineapple including the stem, crown leaves and true leaves. Bromelain is a protease which hydrolyzes proteins present in the juice and, in a higher proportion, in the chicken manure (49). Since chicken manure protein content in relatively high, mixes 1 and 2 with a higher chicken manure concentration, provide a higher biogas yield.
These results are in part a consequence of the enhanced hydrolysis of the protein content, but also a result of the codigestion. Anaerobic codigestion improves the digestibility of carbohydrates present in the lignocellulosic material waste and reduces ammonia accumulation avoiding process instability, by balancing the carbon/nitrogen ratio in the substrate (50). Experimental assays showed that mix 1 was able to produce an average of 692 NL/kg VS, while mix 2 was able to produce 678 NL/kg VS. These differences between mix 1 and 2 are considered non relevant (around 2 %) which leads to choose mix 2 as a better system, because of its lower chicken manure content. In this case, the primary objective of the anaerobic digestion process is to utilize pineapple waste, so a higher pineapple leaf juice content is desirable. On the other hand, chicken manure has a higher acquisition cost, which makes mix 1 have a higher production cost compared to mix 2.
3.2. Techno-economic Analysis
For the techno-economic analysis, a mass balance was carried out to obtain the calculation basis for the economic feasibility analysis. The extraction yield was calculated according to (20) and the biogas production yield was estimated using the experimental data available for the 80/20 mix. Digestate was not quantified during these experiments, so it is not considered in the revenue, but in a real application, this by-product can be sold for soil remediation applications. The mass balance is presented in Fig. 3.
The pineapple leaves are collected in the field and transported to the processing plant, where the wet leaves are crushed with a mechanical extractor to separate the juice from the wet fiber. During this process, (42) estimate a loss of 3 kg of wet leaves per 60 kg of processed leaves, as well as a juice yield of 77 % of the initial feed. This implies that the 250 ton/day of wet leaves used as the calculation basis generate about 192 ton/day of juice. Given that the juice is fed into the reactor in an 80 % proportion with 20 % chicken manure, the process needs around 48 ton/day of this solid residue.
The obtained juice and the chicken manure are pumped into the reactor. The reactor, pumps and pipe system were selected based on the 15 days of hydraulic retention time and daily feed process. According to the experimental results, an estimate of almost 22 000 m3/day of biogas are expected.
The described process is technically feasible according to the experimental results shown in the previous section, but economic feasibility is a crucial factor to determine the viability
of this waste management process. The economic evaluation results, shown in TABLE VII, give a CapEx of US$ 1 283 382 for the implementation of the processing plant. This is a relatively low investment, considering that the OpEx is US$ 3 598 455, which includes raw materials, electricity, maintenance, and labor. Considering that a very large amount of biomass must be collected and transported, raw materials cost is a significant contribution in the production cost. However, another high contribution to the operation costs is utilities, which is to be expected since mechanical extraction of the juice is an energy-intensive process (42). For these results, the equipment cost considers an anaerobic reactor, with a heating system and stirring mechanism, the juice extractor and a centrifugal pump.
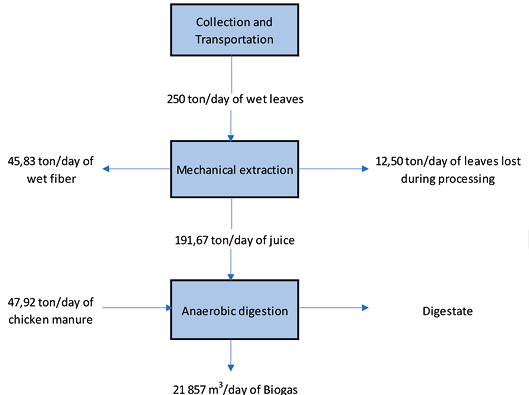
Fig. 3. Fig. 3. Mass balance for the anaerobic digestion of pineapple juice obtained from the processing of 250 tons/day of pineapple leaves.
The payback time can be even more attractive since other by-products, like fiber and digestate can also be commercialized as value-added products with low extra treatments required. These preliminary results show great promise, but a detailed feasibility study is recommended to reduce investment risks.
TABLE VII ECONOMIC PERFORMANCE OF ANAEROBIC CODIGESTION PROCESS FOR 192,5 METRIC TONS PER DAY OF PINEAPPLE LEAVES JUICE WITH 48,1 METRIC TONS OF CHICKEN MANURE
Category | Cost | Units | Reference |
Direct Costs | |||
Equipment cost | |||
Juice extra | 50 000 | US$ | (42) |
Centrifugal Pump | 10 300 | US$ | (51) |
Anaerobic reactor with mixer | 69 400 | US$ | |
Total equipment cost | 129 700 | US$ | - |
Equipment local taxes and international delivery | 194 550 | US$ | (41) |
Equipment installation | 91 439 | US$ | (41) |
Instrumentation and controls (installed) | 70 038 | US$ | (41) |
Piping (installed) | 132 294 | US$ | (41) |
Electrical systems (installed) | 21 400 | US$ | (41) |
Buildings (with services) | 35 019 | US$ | (41) |
Yard improvements | 19 455 | US$ | (41) |
Service facilities (installed) | 136 185 | US$ | (41) |
Indirect costs | |||
Engineering and supervision | 64 202 | US$ | (41) |
Construction expenses | 79 765 | US$ | (41) |
Legal expenses | 7 782 | US$ | (41) |
Contractor’s fee | 42 801 | US$ | (41) |
Contingency | 85 602 | US$ | (41) |
Fixed capital investment | 1 110 232 | US$ | - |
Working capital | 173 150 | US$ | - |
Total capital investment | 1 283 381 | US$ | - |
Operating costs | |||
Labor | 51 898 | US$ /year | - |
Maintenance | 64 169 | US$ /year | (41) |
Utilities | 1 520 647 | US$ /year | - |
Raw materials | 1 961 741 | US$ /year | - |
Total operating costs | 3 598 455 | US$ /year | - |
Total Product Sales | 4 166 590 | US$ /year | - |
Net Revenue A | 568 135 | US$ /year | - |
Payback Time | 2,3 | years | - |
A: Estimated revenue from biogas considers a sale price of US$ 0,49 per kg of biogas(local cost of 1 MJ equivalent from a gaseous fuel)
4. CONCLUSION
Anaerobic codigestion of pineapple leaves juice with chicken manure at a 70/30 proportion gives the highest amount of biogas generation between the studied combinations, for an average of 692 NL/kg VS, however the mix with an 80/20 proportion produced only 2 % less biogas on average. In both cases, a higher biogas yield was obtained compared to the 100 % chicken manure (608 NL/kg VS) and 100 % pineapple leaves juice (231 NL/kg VS). These results reinforce the increase in biogas yield obtained during codigestion processes, as well as the increased biodegradability, compared to the mono-digestion alternative. The use of chicken manure balances the C/N ratio and the pineapple leaves juice provides the mix with proteolytic enzymes that increase the material degradation. According to the results obtained in the techno-economic study, anaerobic codigestion of these two substrates is technically and economically feasible, resulting in a payback time of 2,3 years.
5. ACKNOWLEDGEMENTS
The authors would like to thank the University of Costa Rica for the financial support, as well as undergraduate assistants that participated in the data gathering for the experimental section.
Roles
Juliana Da Luz Castro: Data curation, Formal analysis, Research, Methodology, Writing – original draft, Visualization
Juan Pablo Rojas Sossa: Conceptualization, Data curation, Formal analysis, Fund acquisition, Research, Methodology, Resources, Supervision, Writing – review and editing
Mauricio Bustamante Román: Conceptualization, Data curation, Funding acquisition, Research, Methodology, Project administration, Supervision, Validation – Verification, Visualization, Writing – review and editing